Cast aluminum and wrought iron have some similarities in their functionality in everyday life. Depending on the use for the material, each can serve a unique purpose.
Primarily, wrought iron is used for fencing, gates, tools and equipment such as nails, steam pipes, and ornamental ironwork. Cast aluminum is mostly seen in kitchenware products as well as internal automotive parts.
While wrought iron is a stronger, denser material, cast aluminum has paved its way as a necessary common material in many households today. In this article, you’ll find an in-depth look at each material and the uses for each.
Table of Contents
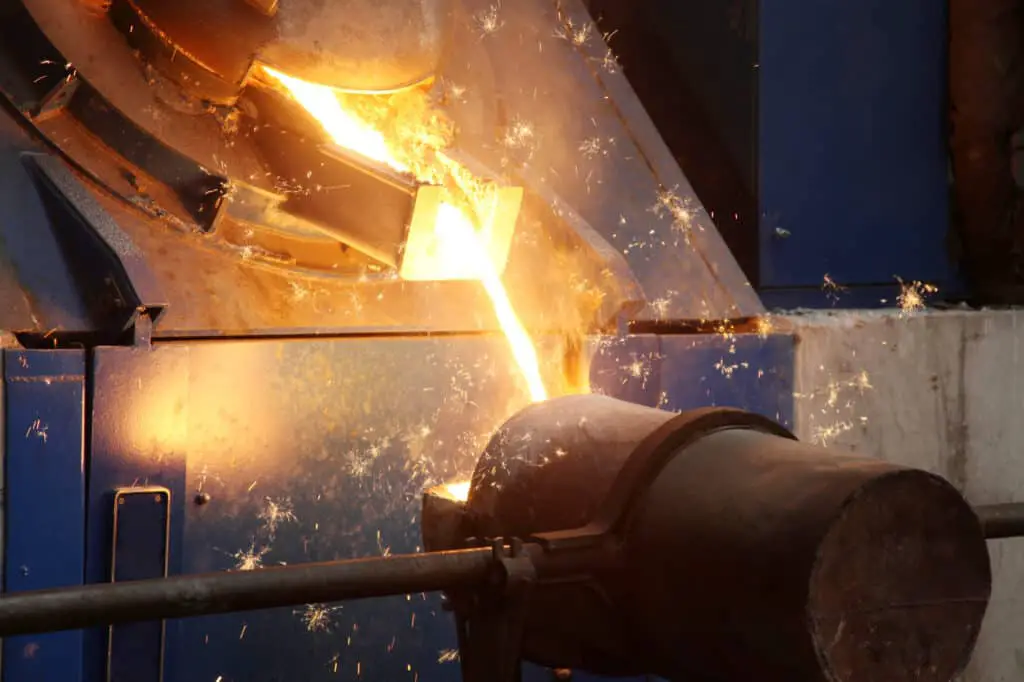
Cast Aluminum vs. Wrought Iron
Through technological advancements, cast aluminum has been a highly cost-effective and carbon-friendly material used to make everyday products.
Without the presence of wrought iron, however, cast aluminum would not be around today. Wrought iron’s advantages are that by itself, it has excellent weldability, strength, and can be forged easily.
However, in today’s day and age, we’re looking for strength but also cost-efficient means for our goods. Cast aluminum may not be as physically strong as wrought iron but contains equal amount of heat-resistant and corrosion-resistant properties.
Depending on the infrastructure or product, use of cast aluminum and wrought iron will always be up against each other. However, cast aluminum offers a faster, more efficient, and more carbon-friendly product than wrought iron does.
While wrought iron’s physicality and denseness provide a material that can withstand great duress, it is not as malleable as cast aluminum. Since cast aluminum has different processes depending on the need for the aluminum, it is a more widely used material for today’s needs.
Wrought Iron Overview
Iron dates back to the ancient Egyptians, around 3200 B.C. In the beginning, even the origin of iron, civilizations were using iron for main weaponry and believe it or not, iron was founded from meteorites.
As an essential element and one found from the Earth, iron has prevailed as one of the strongest material for building infrastructure.
Since the Iron Age, iron has been a crucial need for civilizations across the globe. After learning that adding heat to iron and being able to “work” it and in turn make it “wrought,” iron became much more of an everyday and highly commodified material.
Because of its longstanding history and longevity, engineers and manufacturers turn to wrought iron for many different uses and needs today.
Wrought iron is used widely today for security purposes including gates, fences, and security doors. Because it can withstand great physical duress, wrought iron is still heavily sought after and utilized today.
Cast Aluminum Overview
What is it? You have probably heard of cast aluminum or read about it on certain pieces that exist in your home. Casting aluminum is the most widely used method for aluminum products today.
It works like any casting process: molten aluminum is poured into a mold for a desired pattern. Many products including patio furniture, kitchen cookware, and automobile parts are manufactured by cast aluminum.
Aluminum is the most commonly cast non-ferrous metal in the world. There are a few reasons why it has received accolades and usage in today’s modern world. Aluminum, at its core, is a lightweight metal making it easy to cast and turn into a more malleable product.
There are different casting processes when it comes to aluminum. The three main processes are die casting, permanent mold casting, and sand casting.
Die Casting
Die casting is the process of taking molten metals into a mold-form using high pressure and high-heat. Die casting began in the early 1800s and was primarily used for the printing industry.
In 1849, Sturges, created the first manually operated machine for a casting type. This development showed how accurate a specific mold, using die casting, could work. It was a major advancement in how aluminum could be utilized for everyday use.
Advantages of Die Casting
Die casting is one of the more commonly used applications of aluminum casting today. The process is highly cost-effective and allows for a high volume of parts to be produced very quickly.
The other advantages include that the product is lightweight, yet still durable. Die casting creates an aluminum resistant to corrosion and excellent electric conductivity.
Another popular reason for the die casting method is how fully recyclable and reusable every product involved is in production.
Permanent Mold Casting
Permanent Mold Casting, or Gravity Die Casting, is similar in process to die casting, but utilizes the force of gravity to create its product.
Advantages of Permanent Mold Casting
Permanent Mold Casting is the same process as die casting, except for one difference. Permanent mold casting uses gravity as the only force, allowing the molten aluminum to achieve a more natural fill to the mold.
Permanent mold casting is used primarily for companies that require over 5,000 or more pieces of the product within a year. It is generally a better type of casting because of its natural form-fitting ability and is also highly cost-effective.
Sand Casting
Sand Casting is the oldest form of aluminum casting and can be traced back to 1000 B.C. The process, “Sand Casting,” derives its name because the mold that the aluminum is poured into is primarily made of compressed or compacted sand.
Sand casting is the most popular use of aluminum casting today and has the most versatile features of the different casting processes.
Advantages of Sand Casting
Sand Casting is the most historic way to cast aluminum and still regarded as the most efficient way for casting today. While the process of sand casting is slower than permanent mold casting or die casting, it is a more economical way of casting aluminum.
The other advantage of sand casting is that the individual can create an intricate design for their final product.
Virtually any design can be made through sand casting. Sand casts are usually larger than the final product to allow for shrinkage and cooling while the aluminum solidifies.
Where Do I See Cast Aluminum in my Everyday Life?
Primarily, cast aluminum is seen in automotive parts to improve the fuel-efficiency of vehicles. Because of its lightweight nature, cast aluminum is also prevalent in the telecom and computing industries.
In your home today, it is likely that you would find some cookware that is cast aluminum. It became a popular material in cookware for a few reasons. We know that its lightweight, and also heat resistant.
Cast aluminum is also scratch-resistant, durable, won’t rust, and releases food easily.
Where Do I See Wrought Iron in my Everyday Life?
Iron is seen almost as commonly as cast aluminum but today is most often disguised as stainless steel or iron-based product.
Wrought iron is used heavily in infrastructure and design and when turned into steel with the addition of carbon, can be found in everyday tools, kitchenware, and security products.
Final Thoughts
Wrought iron is a denser and stronger material, but cast aluminum has it’s place, especially in the kitchen.
Which one is better?
Well, it depends on what you need it for and what you’ll be doing with it. Wrought iron is great for, say, fences, whereas cast aluminum can be used to make excellent kitchen parts, as well as automotive parts used inside the car.
Continue Reading: